As the automotive industry undergoes a seismic shift towards electric vehicles (EVs), the demand for efficient and innovative production processes in sheet metal fabrication is more critical than ever. This evolution is driven by the unique requirements of EVs, including weight reduction, enhanced safety, and integration of advanced technologies.
This article explores these key trends shaping the future of sheet metal fabrication for electric vehicles.
1. Advanced Manufacturing Techniques
1.1 Additive Manufacturing and Hybrid Processes
Integrating additive manufacturing (3D printing) with traditional sheet metal processes is gaining traction. Hybrid manufacturing techniques enable the production of intricate geometries that were once difficult to accomplish using traditional methods. This can lead to lightweight components that enhance vehicle performance and efficiency.
1.2 Automation and Robotics
Automated systems efficiently handle repetitive tasks like cutting, bending, and welding, minimizing human error and boosting production speed. Additionally, collaborative robots (cobots) are increasingly prevalent, working alongside human operators to enhance both productivity and safety.
2. Smart Manufacturing and Industry 4.0
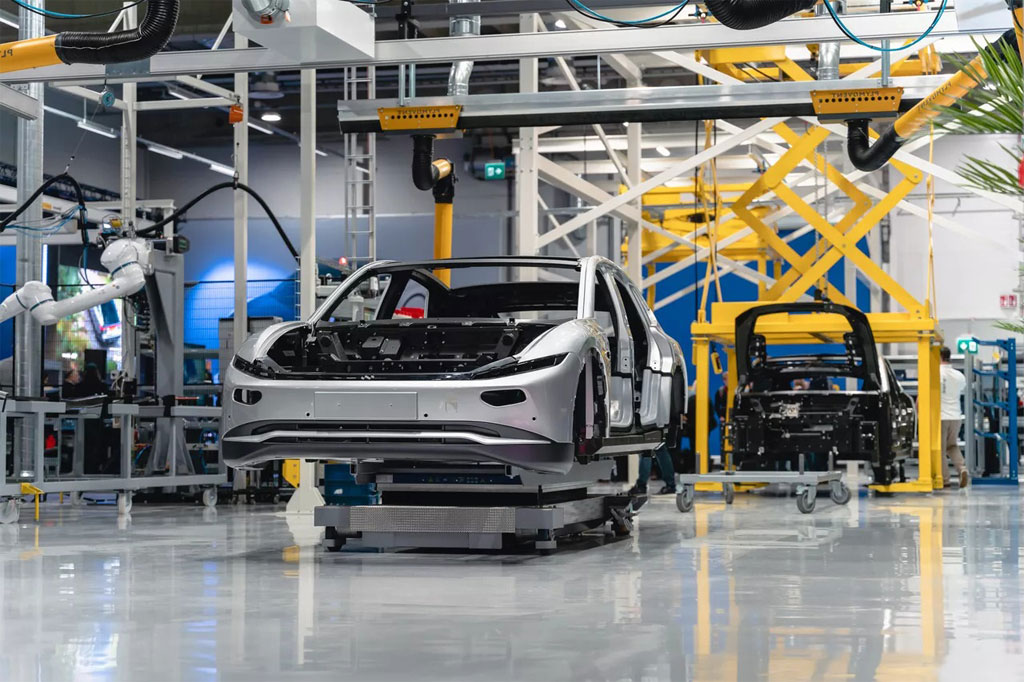
2.1 Data-Driven Decision Making
Integrating IoT (Internet of Things) devices into sheet metal fabrication real-time monitoring and data collection. This data-driven strategy empowers manufacturers to optimize production processes, anticipate maintenance requirements, and enhance quality control. By leveraging predictive analytics, companies can minimize downtime and boost overall efficiency.
2.2 Digital Twin Technology
Creating digital twins of fabrication processes provides manufacturers with a virtual representation of their operations. This allows for better planning, testing, and optimization of workflows before implementation in the physical environment. As EV designs become more complex, digital twins will play a vital role in streamlining production.
3. Sustainable Practices
3.1 Recycling and Material Efficiency
Sustainability is central to the future of the automotive industry, and sheet metal fabrication is no exception. Methods that enhance material efficiency, such as nesting optimization and scrap reduction strategies, are being widely implemented. Furthermore, recycling metal scraps back into the production process helps minimize waste and lower the carbon footprint.
3.2 Use of Lightweight Materials
As EVs require lightweight components to enhance battery efficiency, the use of advanced materials like high-strength aluminum and specialized alloys is on the rise. Fabrication processes are adapting to handle these materials, necessitating new techniques and equipment to ensure quality and performance.
4. Enhanced Safety and Quality Control
4.1 Incorporation of Safety Standards
Electric vehicles (EVs) are typically outfitted with advanced safety features, necessitating that their components adhere to strict safety regulations. Automated inspection systems using machine vision can reliably verify that parts consistently meet quality standards.
4.2 Simulation and Testing
Prior to production, simulation tools can be used to test the performance of sheet metal designs under various conditions. This allows manufacturers to identify potential issues and make necessary adjustments, resulting in higher-quality components that align with the safety and performance expectations of modern EVs.
Conclusion
The future of sheet metal fabrication for electric vehicles is poised for transformative change. By embracing advanced manufacturing techniques, smart technologies, sustainable practices, and rigorous quality control, manufacturers can meet the demands of an evolving automotive landscape.
As the industry continues to innovate, those who adapt to these trends will position themselves at the forefront of the electric vehicle revolution, driving both efficiency and sustainability in production processes.
As the automotive industry undergoes a seismic shift towards electric vehicles (EVs), the demand for efficient and innovative production processes in sheet metal fabrication is more critical than ever. This evolution is driven by the unique requirements of EVs, including weight reduction, enhanced safety, and integration of advanced technologies. Here, we explore the key trends shaping the future of sheet metal fabrication for electric vehicles.
1. Advanced Manufacturing Techniques
Additive Manufacturing and Hybrid Processes
Integrating additive manufacturing (3D printing) with traditional sheet metal processes is gaining traction. Hybrid manufacturing techniques allow for the creation of complex geometries that were previously challenging to achieve with conventional methods. This can lead to lightweight components that enhance vehicle performance and efficiency.
Automation and Robotics
The adoption of automation and robotics in fabrication processes is increasing. Automated systems streamline repetitive tasks such as cutting, bending, and welding, reducing human error and improving production speed. Collaborative robots (cobots) are also becoming common, working alongside human operators to enhance productivity and safety.
2. Smart Manufacturing and Industry 4.0
Data-Driven Decision Making
The implementation of IoT (Internet of Things) devices in sheet metal fabrication allows for real-time monitoring and data collection. This data-driven approach enables manufacturers to optimize production processes, predict maintenance needs, and improve quality control. Predictive analytics can reduce downtime and enhance overall efficiency.
Digital Twin Technology
Creating digital twins of fabrication processes provides manufacturers with a virtual representation of their operations. This allows for better planning, testing, and optimization of workflows before implementation in the physical environment. As EV designs become more complex, digital twins will play a vital role in streamlining production.
3. Sustainable Practices
Recycling and Material Efficiency
Sustainability is at the forefront of the automotive industry’s future, and sheet metal fabrication is no exception. Techniques that maximize material efficiency, such as nesting optimization and scrap reduction strategies, are increasingly being adopted. Additionally, the recycling of metal scraps back into the production cycle minimizes waste and reduces the carbon footprint.
Use of Lightweight Materials
As EVs require lightweight components to enhance battery efficiency, the use of advanced materials like high-strength aluminum and specialized alloys is on the rise. Fabrication processes are adapting to handle these materials, necessitating new techniques and equipment to ensure quality and performance.
4. Enhanced Safety and Quality Control
Incorporation of Safety Standards
As EVs are often equipped with advanced safety features, the fabrication of components must meet stringent safety regulations. Automated inspection systems utilizing machine vision can ensure that parts meet quality standards consistently. This reduces the risk of defects and enhances the overall safety of the vehicle.
Simulation and Testing
Prior to production, simulation tools can be used to test the performance of sheet metal designs under various conditions. This allows manufacturers to identify potential issues and make necessary adjustments, resulting in higher-quality components that align with the safety and performance expectations of modern EVs.
Conclusion
The future of sheet metal fabrication for electric vehicles is poised for transformative change. By embracing advanced manufacturing techniques, smart technologies, sustainable practices, and rigorous quality control, manufacturers can meet the demands of an evolving automotive landscape. As the industry continues to innovate, those who adapt to these trends will position themselves at the forefront of the electric vehicle revolution, driving both efficiency and sustainability in production processes.
As the automotive industry undergoes a seismic shift towards electric vehicles (EVs), the demand for efficient and innovative production processes in sheet metal fabrication is more critical than ever. This evolution is driven by the unique requirements of EVs, including weight reduction, enhanced safety, and integration of advanced technologies. Here, we explore the key trends shaping the future of sheet metal fabrication for electric vehicles.
1. Advanced Manufacturing Techniques
Additive Manufacturing and Hybrid Processes
Integrating additive manufacturing (3D printing) with traditional sheet metal processes is gaining traction. Hybrid manufacturing techniques allow for the creation of complex geometries that were previously challenging to achieve with conventional methods. This can lead to lightweight components that enhance vehicle performance and efficiency.
Automation and Robotics
The adoption of automation and robotics in fabrication processes is increasing. Automated systems streamline repetitive tasks such as cutting, bending, and welding, reducing human error and improving production speed. Collaborative robots (cobots) are also becoming common, working alongside human operators to enhance productivity and safety.
2. Smart Manufacturing and Industry 4.0
Data-Driven Decision Making
The implementation of IoT (Internet of Things) devices in sheet metal fabrication allows for real-time monitoring and data collection. This data-driven approach enables manufacturers to optimize production processes, predict maintenance needs, and improve quality control. Predictive analytics can reduce downtime and enhance overall efficiency.
Digital Twin Technology
Creating digital twins of fabrication processes provides manufacturers with a virtual representation of their operations. This allows for better planning, testing, and optimization of workflows before implementation in the physical environment. As EV designs become more complex, digital twins will play a vital role in streamlining production.
3. Sustainable Practices
Recycling and Material Efficiency
Sustainability is at the forefront of the automotive industry’s future, and sheet metal fabrication is no exception. Techniques that maximize material efficiency, such as nesting optimization and scrap reduction strategies, are increasingly being adopted. Additionally, the recycling of metal scraps back into the production cycle minimizes waste and reduces the carbon footprint.
Use of Lightweight Materials
As EVs require lightweight components to enhance battery efficiency, the use of advanced materials like high-strength aluminum and specialized alloys is on the rise. Fabrication processes are adapting to handle these materials, necessitating new techniques and equipment to ensure quality and performance.
4. Enhanced Safety and Quality Control
Incorporation of Safety Standards
As EVs are often equipped with advanced safety features, the fabrication of components must meet stringent safety regulations. Automated inspection systems utilizing machine vision can ensure that parts meet quality standards consistently. This reduces the risk of defects and enhances the overall safety of the vehicle.
Simulation and Testing
Prior to production, simulation tools can be used to test the performance of sheet metal designs under various conditions. This allows manufacturers to identify potential issues and make necessary adjustments, resulting in higher-quality components that align with the safety and performance expectations of modern EVs.
Conclusion
The future of sheet metal fabrication for electric vehicles is poised for transformative change. By embracing advanced manufacturing techniques, smart technologies, sustainable practices, and rigorous quality control, manufacturers can meet the demands of an evolving automotive landscape. As the industry continues to innovate, those who adapt to these trends will position themselves at the forefront of the electric vehicle revolution, driving both efficiency and sustainability in production processes.
As the automotive industry undergoes a seismic shift towards electric vehicles (EVs), the demand for efficient and innovative production processes in sheet metal fabrication is more critical than ever. This evolution is driven by the unique requirements of EVs, including weight reduction, enhanced safety, and integration of advanced technologies. Here, we explore the key trends shaping the future of sheet metal fabrication for electric vehicles.
1. Advanced Manufacturing Techniques
Additive Manufacturing and Hybrid Processes
Integrating additive manufacturing (3D printing) with traditional sheet metal processes is gaining traction. Hybrid manufacturing techniques allow for the creation of complex geometries that were previously challenging to achieve with conventional methods. This can lead to lightweight components that enhance vehicle performance and efficiency.
Automation and Robotics
The adoption of automation and robotics in fabrication processes is increasing. Automated systems streamline repetitive tasks such as cutting, bending, and welding, reducing human error and improving production speed. Collaborative robots (cobots) are also becoming common, working alongside human operators to enhance productivity and safety.
2. Smart Manufacturing and Industry 4.0
Data-Driven Decision Making
The implementation of IoT (Internet of Things) devices in sheet metal fabrication allows for real-time monitoring and data collection. This data-driven approach enables manufacturers to optimize production processes, predict maintenance needs, and improve quality control. Predictive analytics can reduce downtime and enhance overall efficiency.
Digital Twin Technology
Creating digital twins of fabrication processes provides manufacturers with a virtual representation of their operations. This allows for better planning, testing, and optimization of workflows before implementation in the physical environment. As EV designs become more complex, digital twins will play a vital role in streamlining production.
3. Sustainable Practices
Recycling and Material Efficiency
Sustainability is at the forefront of the automotive industry’s future, and sheet metal fabrication is no exception. Techniques that maximize material efficiency, such as nesting optimization and scrap reduction strategies, are increasingly being adopted. Additionally, the recycling of metal scraps back into the production cycle minimizes waste and reduces the carbon footprint.
Use of Lightweight Materials
As EVs require lightweight components to enhance battery efficiency, the use of advanced materials like high-strength aluminum and specialized alloys is on the rise. Fabrication processes are adapting to handle these materials, necessitating new techniques and equipment to ensure quality and performance.
4. Enhanced Safety and Quality Control
Incorporation of Safety Standards
As EVs are often equipped with advanced safety features, the fabrication of components must meet stringent safety regulations. Automated inspection systems utilizing machine vision can ensure that parts meet quality standards consistently. This reduces the risk of defects and enhances the overall safety of the vehicle.
Simulation and Testing
Prior to production, simulation tools can be used to test the performance of sheet metal designs under various conditions. This allows manufacturers to identify potential issues and make necessary adjustments, resulting in higher-quality components that align with the safety and performance expectations of modern EVs.
Conclusion
The future of sheet metal fabrication for electric vehicles is poised for transformative change. By embracing advanced manufacturing techniques, smart technologies, sustainable practices, and rigorous quality control, manufacturers can meet the demands of an evolving automotive landscape. As the industry continues to innovate, those who adapt to these trends will position themselves at the forefront of the electric vehicle revolution, driving both efficiency and sustainability in production processes.